Aktuelles: Lectra entwickelt Zuschnittraum für Einzelstücke
Kunden möchten mehr Mitsprache beim Mode- oder Möbelkauf – Einzelstücke in hoher Qualität individuell auf ihre Bedürfnisse zugeschnitten. Eine Herausforderung für die Möbel- und Modehersteller, soll es doch gleichzeitig schnell und kostengünstig sein. Mit dem Cutting Room 4.0 bringt Lectra eine neue digitale Zuschnittlösung für Einzelstücke in Serie auf den Markt und ermöglicht die kundenindividuelle Massenfertigung.
Mitte November 2017 stellte Lectra den neuen Cutting Room 4.0 vor. Mit der Zuschnittlösung ist die wirtschaftliche Fertigung in Losgröße 1 möglich. Der vollständig integrierte Zuschnittraum besteht aus dem Einzellagen-Zuschnitt und einer Cloud-basierten Software-Plattform. Sie ist das Herzstück der Lösung und verknüpft als künstliche Intelligenz (KI) alle Bereiche der Produktion.
Die KI verwaltet eingehende Aufträge und erstellt automatisiert den optimalen Produktionsplan. Sie kennt alle Materialeigenschaften und überblickt Lagerbestände, um Fertigungsaufträge besser einzutakten und den Zuschnitt laufend zu optimieren. Ablaufänderungen bindet sie nahtlos in den Zuschnittprozess ein. Die intelligente Schnittsoftware nutzt den verarbeiteten Stoff optimal aus und spart Herstellungskosten. Durch integrierte Services, wie der vorausschauenden Wartung, hat der Zuschnittraum eine Betriebsbereitschaft von 98 Prozent. Ein Gesamtkonzept vollständig ausgerichtet auf Industrie 4.0, das Unternehmen in ihren IT‑Landschaft integrieren.
„Kunden wollen individualisierte Produkte zu günstigen Preisen“, sagt Helene Kehren, Marketing Manager Furniture CEER bei Lectra Deutschland. „Digitalisierung und Industrie 4.0 machen Unternehmen flexibel genug, diese Erwartungen zu erfüllen. Der neue Cutting Room 4.0 ermöglicht kundenindividuelle Einzelstücke am laufenden Band – in Qualität wie von Handarbeit.“
Markt & Meinung: Von Massenproduktion zur Maß-Produktion
Während er die personalisierten Laufschuhe auszieht und den Maßkonfektions-Anzug von der Stange an, löffelt er den Rest seines online selbst zusammengestellten Müslis. Dabei sucht er mit einer Augmented Reality-App ein neues Sofa, dass sowohl zu seinem Stil passt, als auch in die genau 2,78 Meter breite Lücke zwischen Wand und Bücherregal. Der moderne Kunde steht nicht mehr auf Massenware. Einzelstücke sollen es sein, zum Preis, als seien sie in Masse produziert. Dieser Trend zieht sich bereits durch alle Branchen. Doch nicht alles, was personalisiert ist, ist tatsächlich ein Einzelstück. Das soll sich bald ändern – durch neue Fertigungstechniken.
Die Idee ist nicht neu. Bereits 1992 schrieb der US‑Unternehmensberater B. Joseph Pine II: „Mass customization wird für das 21. Jahrhundert so wichtig sein, wie es die Massenproduktion für das 20. Jahrhundert war.“ Sein Buch Mass Customization: The New Frontier in Business Competition wurde ein Wirtschafts-Bestseller. Der Begriff bezeichnet das serienmäßige Anfertigen von Produkten, einzeln auf die Kundenwünsche zugeschnitten. Der eigentliche Clou: Der Kunde zahlt trotzdem wie vom Band. Vor allem die Generation der Millennials sucht vermehrt nach Möglichkeiten, die eigenen Ideen und Bedürfnisse in Produkte einfließen zu lassen.
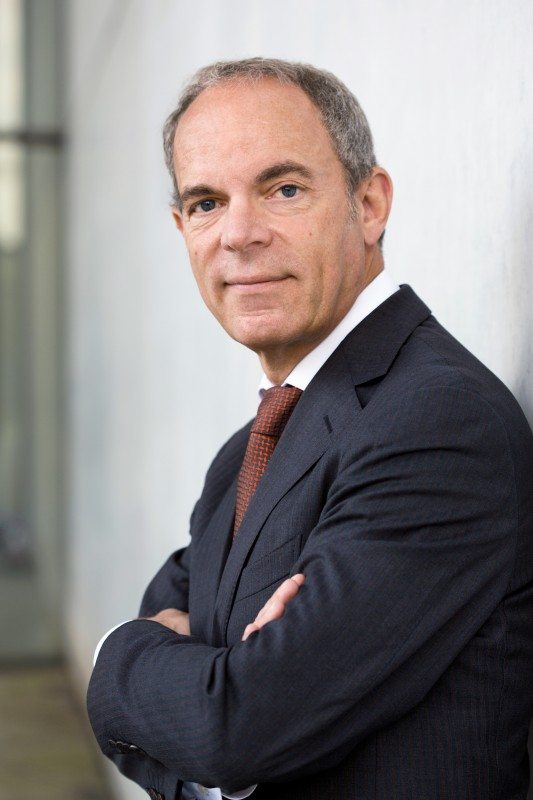
„Kundenindividuelle Massenproduktion ist die Zukunft, aber noch im Marktreifetest“, sagt Chris Nicolaes, Geschäftsführer des Technologie-Experten Lectra Deutschland. „Sie ist ressourcenschonend, da sie nur soviel produziert, wie der Kunde auch kauft. Möglich wird sie durch digitale automatisierte Fertigungstechniken, die Textilien präzise schneiden, Stoffe optimal ausnutzt und so zusätzlich Herstellungskosten sparen.“ Viele der bisherigen personalisierten Angebote beschränken sich auf das Äußerliche der Produkte und sind teils wenig mehr als geschicktes Marketing. Der Pullover, bedruckt mit einem Motiv nach Wahl oder die Trinkflasche mit dem eigenen Namen versehen. Das Grundprodukt bleibt unverändert, die Produktion wird lediglich um einen Schritt erweitert. Dennoch offenbart der Trend, dass die Nachfrage vorhanden und der Markt reif ist für die Maß‑Produktion.
Aus Massenware im Einzeldesign wird Einzelware in Massenproduktion
In der Automobilindustrie stieg etwa nicht nur die Anzahl der vom Hersteller angebotenen Modelle, sondern auch die Optionen, die der Kunde pro Modell hat. Erreicht haben die Autohersteller das durch modulare Produktionsanlagen. So gestalten Autobauer ihre Produkte wesentlich variantenreicher, ohne dass die Produktionskosten dabei ins Unermessliche schießen. Durch die Masse der Optionen entsteht die Quasi‑Kundenindividualität. Der Opel Adam ist ein gutes Beispiel dafür: Käufer haben über eine Million verschiedene Kombinations-möglichkeiten für ihren Neuwagen, Farbe und Interieur ebenso wie Karosserie und eingebaute Technik.

Dem Beispiel der modularen Produktion folgen heute auch andere Branchen. Das eigens kreierte Müsli ebenso wie der selbst designte Laufschuh folgen diesem Prinzip. Doch je komplexer die Ware, je individualisierter sie ist, desto höher steigen auch die Kosten – und desto länger sind die Lieferzeiten. 14 Tage gelten als Obergrenze, die der Kunde gewöhnt ist. Nur bei sehr hochwertigen Gütern, wie Autos, Möbel oder Anzüge, nimmt er auch längeres Warten in Kauf.
Individualität am laufenden Band
„Die richtige Maß‑Produktion beginnt aber erst dort, wo der Kunde die Funktionalität mitbestimmen kann, ohne einschränkende Vorgaben“, sagt Nicolaes. „Um das umzusetzen sind flexible Fertigungsanlagen notwendig, die automatisch die Produktion anpassen, ohne den Prozess zu unterbrechen.“
Den Schritt zur kundenindividuell produzierten Kleidung in Masse geht Dolzer. Das 1963 gegründete Unternehmen spezialisiert sich auf maßgeschneiderte Kleidung für Business, Freizeit, Hochzeiten und Ceremonial. Dazu zählen Anzüge und Hemden für Männer sowie Kostüme und Blusen für Frauen. Wie bei einem traditionellen Schneider wird der Kunde Teil des Herstellungsprozesses. Nach dem Prinzip “made to measure“ wählt der Kunde jedes Details selbst, von Farbe und Muster über Revers, Taschenstiel bis hin zur Knopfanzahl und der Knopflochfarbe.
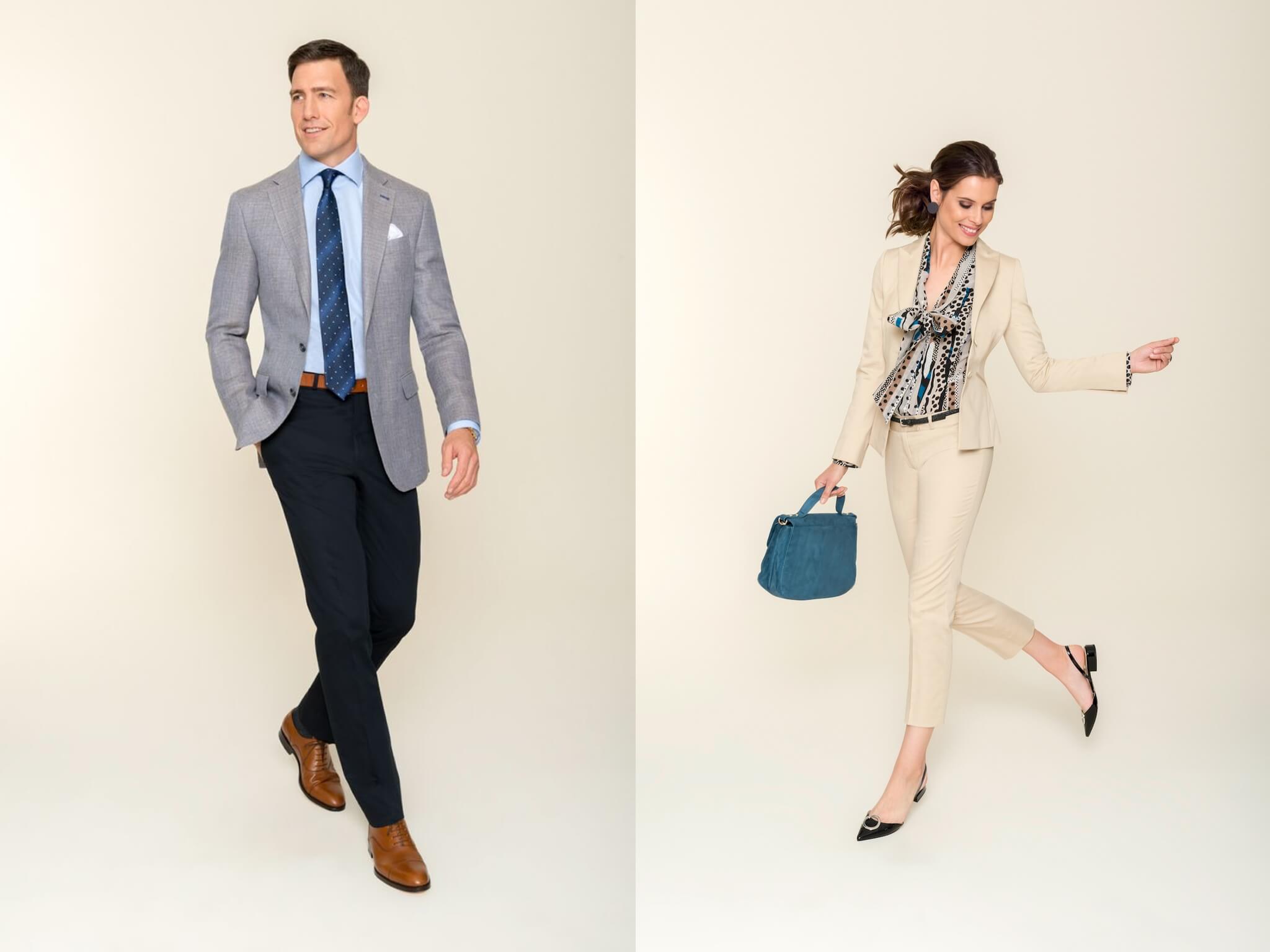
Gemessen wird Zentimeter-genau im Laden. Mehrfachkunden können direkt online mit ihren hinterlegten Maßen bestellen. Das Anfertigen der Einzelteile übernimmt eine automatisierte Zuschnittlösung. Sie ist digital vernetzt und legt die Schnittmuster für einen optimalen Stoffverbrauch fest. Dabei integriert sie jede Einzelanfertigung ohne Abbruch in den Produktionsprozess. Die Zuschnittlösung kommt von Lectra und Dolzer stellt mit ihr kundenindividuelle Einzelstücke am laufenden Band her, zum Preis vergleichbar hochwertiger Massenware.
Mit der neuen Generation der flexiblen Fertigungstechnologien wird die serienmäßige Maß‑Produktion auch in anderen Branchen möglich. Dann zieht der moderne Kunde nicht mehr nur die personalisierten, sondern die maßgefertigten Laufschuhe aus dem 3D-Drucker an und das Zentimeter-genau angefertigte Sofa wird zum IKEA-Preis geliefert.
Wissen Digital: Erweiterte Realität für die Massen
2018 steht – wagt man den Blick in die Glaskugel – im Zeichen der Augmented Reality. Spätestens seit dem globalen Einschlag des Smartphone-Spiels Pokémon Go ist der Effekt der Technologie greifbar. Mehr als Spielerei war es bisher jedoch nicht. Spezielle Hardware brachte eine halbwegs realistische Darstellung auf den Smartphone-Bildschirm, die sich maßstabs- und naturgetreu im Raum bewegen oder platzieren ließ. Apple erweitert mit dem aktuellen mobilen Betriebssystem die Grenzen des Möglichen und macht Augmented Reality massentauglich. Das eröffnet dank Millionen von Smartphone-Besitzern Anwendungshorizonte und beflügelt ganze Industrien.
Bisher war Google mit der Tango-Plattform die treibende Kraft der Augmented Reality auf Smartphones. AR-Technologie samt dem Haken, dass sie lediglich mit einem der zwei erhältlichen und über 500 Euro teuren Smartphones funktioniert, in denen die notwenige Hardware verbaut ist – Bewegungssensoren, zwei Kameralinsen sowie eine Optik, die räumliche Tiefe erkennt. Eine Hürde, die wenige Käufer nehmen.
Aktuell läuft hingegen Apple mit der eigenen AR-Technologie Google den Rang ab. „ARKit“ bietet den Vorteil der reinen Softwarelösung, die ohne spezielle Hardware auskommt. Die eigene Smartphone Kamera samt integriertem Bewegungssensor genügen. Die vergleichsweise geringen Hardware-Anforderungen erfüllen alle Modelle ab dem iPhone 6S. Damit erfasst und berechnet das AR-Kit den Raum und visualisiert darin Objekte maßstabsgetreu. Die Darstellung ist präzise, das Smartphone misst, beispielsweise ganz wie ein Maßband, die Länge eines Regals zentimeter-genau. Integriert im mobilen Betriebssystem iOS 11 ist die AR-Technologie damit auf über 100 Millionen Geräten verfügbar.
Ikea etwa zeigt, was Apples AR-Kit kann. Mit der Augmented Reality App „Ikea Place“ lassen sich mehrere Möbel in den eigenen vier Wänden virtuell aufstellen und ausprobieren – zu 98 Prozent maßstabsgetreu laut dem schwedischen Möbelunternehmen. „Apple hat ein grundlegendes Problem gelöst“, sagt Michael Valdsgaard, Leader Digital Transformation bei Ikea. „Die Technologie wird verändern, wie wir Kaufentscheidungen treffen.“
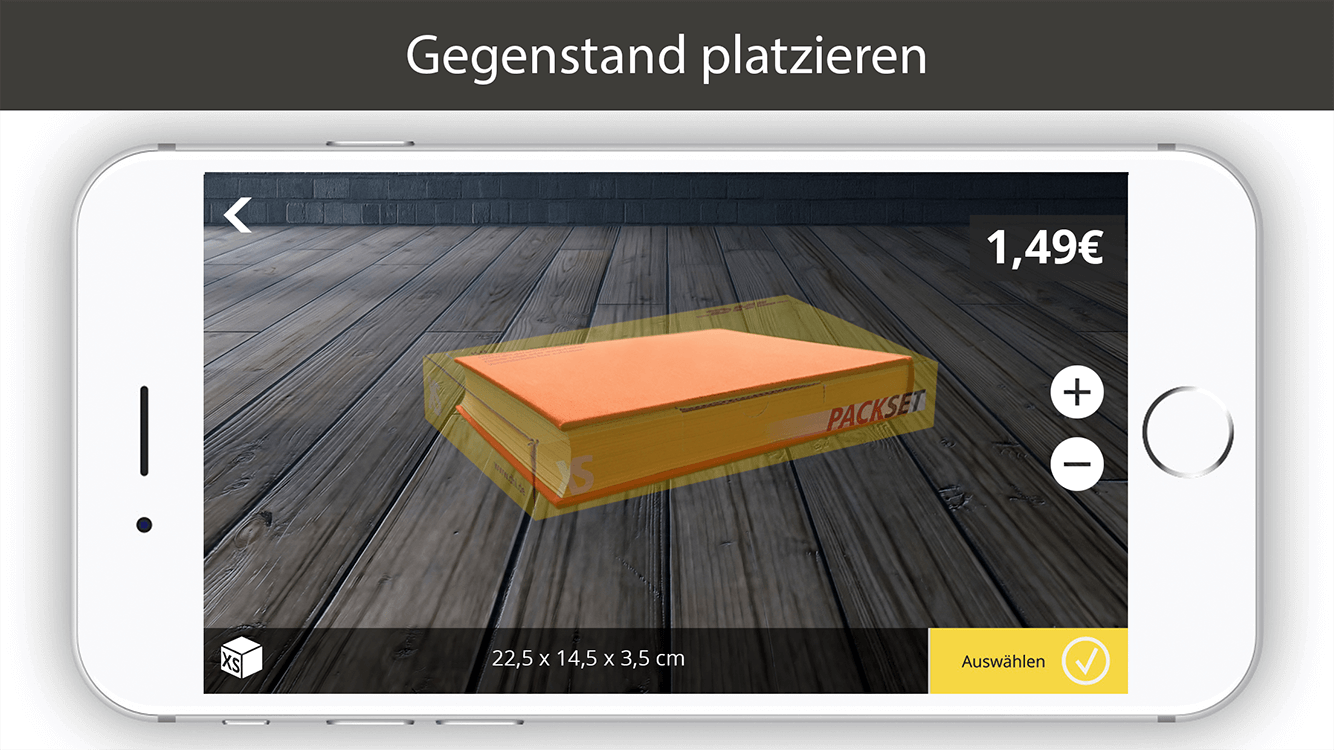
Auch DHL nutzt die neuen Möglichkeiten mittels AR App. Mit „Packset“ projizieren Kunden virtuell unterschiedliche Paketgrößen auf eine Fläche und überprüfen so, ob in das Paket passt, was sie versenden möchten. Das passende Porto mit inbegriffen.
In 2018 verdoppelt sich das Marktpotential. Denn Google reagiert auf Apples Vorstoß mit dem Projekt „ARCore“. Wie bei Apples System ist damit keine Zusatz-Hardware für AR-Anwendungen mehr nötig. Bis Ende 2017 will Google die Software auf über 100 Millionen Android Geräte bringen.
Den Möglichkeiten, die Entwickler und Unternehmen mit den neuen Augmented Reality Technologien haben, sind keine Grenzen gesetzt. Von der digitalen Anprobe von Kleidungsstücken bis hin zu maßgeschneiderten Produkten, hergestellt anhand der vom Smartphone erfassten Körperdaten. Eines zeigen die neuen Anwendungen jetzt schon: Die Realität erweitert sich für alle.