Aktuelles: Lectra 4.0 – CEO von Lectra stellt neue Unternehmensstrategie vor
Wandel und Fortschritt sind beständige Begleiter der Wirtschaft und Industrie. Mit der Zeit zu gehen heißt nicht nur laufend auf Trends und Veränderungen zu reagieren. Es bedeutet auch der Entwicklung voranzugehen. Dafür ist es wichtig zu wissen, wohin der Weg führt. Auf der Strategie-4.0-Pressekonferenz stellte Daniel Harari, CEO von Lectra, die Unternehmensstrategie für 2017 bis 2019 vor. In enger Zusammenarbeit mit Kunden hat das Unternehmen vier Megatrends identifiziert, die schon heute die Mode-, Automobil- und Möbelindustrie verändern.
Den ersten Megatrend stellt die Generation der Millennials dar. Geboren zwischen 1980 und 2000, und aufgewachsen in der digitalen Welt, repräsentiert diese Generation zwei Milliarden Menschen. Millennials brechen mit alten Regeln und Verhaltensweisen und formulieren neue Ideen – als Arbeitnehmer sowie Käufer. Diese Generation fordert Qualität, Produktpersonalisierung und einen nachhaltigen Umgang mit der Umwelt. Unternehmen müssen sich auf die Bedürfnisse und Anforderungen der Millennials einstellen.
Digitalisierung – Grundlage der vierten industriellen Revolution
Die Digitalisierung der Industrie ist der zweite Megatrend. Begründet in einer ganzen Bandbreite neuer Technologien hat die Digitalisierung von Prozessen und Objekten einen stärkeren Einfluss auf Wirtschaft und Industrie als das Internet. Die Analyse der generierten Daten – Big Data – eröffnet neue Möglichkeiten bisherige Strukturen zu verbessern und neue Geschäftsmodelle aufzubauen.
Der dritte Megatrend: Der Umstieg zur Industrie 4.0. Die vierte industrielle Revolution basiert auf der Digitalisierung von industriellen Prozessen, vom Design bis zur Produktion, und der vernetzten Kommunikation zwischen allen Teilen einer Wertschöpfungskette – vom Mitarbeiter über intelligente Maschinen bis hin zum Endkunden.
Europäisches Know-how für China
Der vierte Trend ist die Neuausrichtung der chinesischen Wirtschaft. Chinas Wirtschaft wächst. Das Land ist nicht mehr nur die ausgelagerte Werkbank der Welt, sondern setzt auf Entwicklung und qualitative Produktion für den eigenen Bedarf. Mit dem Programm „Made in China 2025“ verfolgt die Regierung die Modernisierung der chinesischen Industrie. Sie will die eigene Wirtschaft schnell voran bringen auf ihrem Weg zu einer intelligenten, digitalen Industrieproduktion mit hoher Wertschöpfung. Das deutsche Industrie-4.0-Konzept ist dafür die Grundlage.
Lectras Soft- und Hardwarelösungen sind schon heute auf diese Trends ausgerichtet und bereit für die Industrie 4.0. Mit dem Start des SaaS‑Angebots (Software as a Service) seiner Lösungen im kommenden Jahr bringt das Unternehmen zusätzliche Flexibilität in die Wertschöpfungskette der Kunden. „Wir befinden uns in einer unbeständigen Welt, in der Unternehmen flexibel auf rasche Veränderungen reagieren müssen. Mit unseren Soft- und Hardwarelösungen sowie unserem Branchen‑Know-how sind Lectras Kunden bereit für diese Herausforderungen. Die aktuelle Unternehmensstrategie bildet dafür die Grundlage“, schloss Daniel Harari.
Markt & Meinung: Tradition in digital
Traditionsunternehmen sind die Zugpferde der Industrie. Über Jahrzehnte haben sie ihr Kerngeschäft und sichere Strukturen aufgebaut und sich als verlässlicher Partner für Zulieferer und Kunden etabliert. Doch die Industrie ist im digitalen Zeitalter angekommen und stellt Traditionsunternehmen vor die Frage: Weiter auf die bestehenden Strukturen setzen oder Geschäftsmodell und Prozesse digitalisieren? Laut der Kreditanstalt für Wiederaufbau (basierend auf einer Studie des Zentrum für Europäische Wirtschaftsforschung) trieben in den Jahren 2013 bis 2015 rund 83 Prozent der mittelständischen Unternehmen die Digitalisierung innerhalb des Unternehmens voran – aus gutem Grund. Die Umstellung bringt Vorteile.
Möbel in digital
Godfrey Syrett wurde 1947 im Nachkriegsengland gegründet. Damals produzierte der Möbelhersteller in erster Linie für den staatlichen Gesundheitsdienst. Heute bietet das Traditionsunternehmen hochwertige Einrichtungslösungen auch für Bildungseinrichtungen und Büros. Seit der Gründung des Unternehmens hat sich der Möbelmarkt stark verändert.
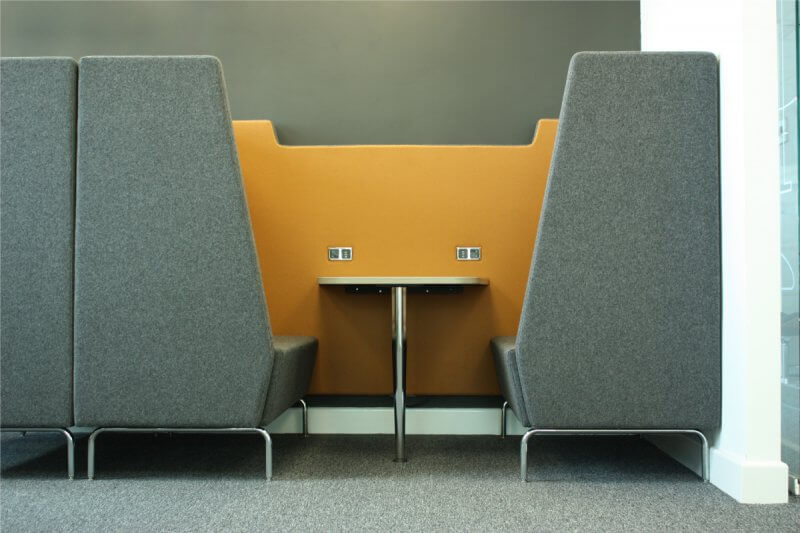
Das heutige Arbeitsumfeld ist von einer hohen Mobilität geprägt und Einrichtungsmöbel müssen flexibel und funktional, aber auch modern und designorientiert sein. Gleichzeitig steigt der Anspruch der Kunden hinsichtlich Qualität und Lieferzeiten. Der manuelle Fertigungsprozess ist nicht mehr geeignet diesen Anforderungen gerecht zu werden. Um die Markteinführungszeit bei gleichbleibender Qualität zu verkürzen und die Produktpalette flexibel weiterentwickeln zu können, digitalisierte Godfrey Syrett seine gesamten Vorproduktions- und Produktionsprozesse. Die Mitarbeiter erstellen heute die Schnittmuster der Textilmöbel digital und der Zuschnitt läuft automatisch. Der Möbelhersteller erhöhte dadurch seine Produktionskapazität um 70 Prozent. Durch den automatisierten Zuschnitt spart das Unternehmen jährlich Material im Wert von 170.000 Euro ein. Das wirkt sich nicht nur positiv auf die Rentabilität von Godfrey Syrett aus. „Wir haben hart daran gearbeitet, unseren negativen Umwelteinfluss zu verringern. Dafür wurden wir kürzlich mit zwei Preisen für nachhaltige Produktion ausgezeichnet. Mithilfe der Lectra-Lösungen haben wir die Materialverschwendung um 20 bis 30 Prozent reduziert und somit unser Engagement für mehr Nachhaltigkeit verstärkt“, sagt David Hall, Vertriebs- und Marketing-Leiter bei Godfrey Syrett.
Leder auf Knopfdruck
Vor allem Großkonzerne der Automobilindustrie setzen schon längst auf eine digitale Wertschöpfungskette. Audi geht bereits einen Schritt weiter und baut seine High‑End-Modelle in einer Smart Factory (lesen Sie mehr dazu in „Wissen Digital“). Zulieferer müssen mit dem Wandel gehen, um nicht den Anschluss zu verpassen. Eine der führenden europäischen Gerbereien für die Automobilindustrie geht mit und digitalisiert ihren Lederzuschnitt. 1958 gegründet betreibt die italienische Gruppo Mastrotto eines der größten Just-in-time-Logistikdrehkreuze der Lederbranche und garantiert eine Lieferzeit von maximal 48 Stunden. Von 20 Produktions- und Logistikstandorten in Italien und weltweit liefert das Traditionsunternehmen jährlich 21 Millionen Quadratmeter Leder an seine Kunden. Die fortschreitenden Individualisierungswünsche der Autokäufer – und damit der Autobauer – führen durch immer mehr Produktvarianten und schnelleren Produktwechseln zu einer höheren Komplexität in der Wertschöpfungskette. Um auf diese Entwicklung einzugehen, setzt Gruppo Mastrotto ebenfalls auf die Digitalisierung mit Lectras Lederzuschnitt-Lösung Versalis. Der digitale Zuschnittraum ermöglicht es, Häute unterbrechungsfrei auf höchstem Qualitätsniveau zu schneiden, die Kapazität zu erhöhen, und dabei Kosten zu sparen. „Automobilteile zu liefern ist nicht nur ein Abarbeiten von Aufträgen“, sagt Alberto Silvagni, Automotive General Manager der Gruppo Mastrotto. „Es geht darum, die veränderten Kundenbedürfnisse hinsichtlich Design und Volumen zu erfüllen. Mit unseren alten Stanzmaschinen hätten wir die neuen Anforderungen der OEMs niemals so erfüllen können wie mit unseren neuen digitalen Lösungen.“
Mode mit Touch
Die Nachfrage nach individualisierten Produkten mit hoher Qualität zu günstigen Preisen steigt vor allem auch in der Modebranche. „Fast Fashion ist ein erfolgreiches Konzept, das diesen Käuferwünschen entspricht. High End-Entwürfe werden aufgenommen, in lediglich zwei bis drei Wochen vom Zeichenbrett an die Stange gebracht und weltweit zu erschwinglichen Preisen verkauft“, erklärt Chris Nicolaes, Geschäftsführer Lectra Deutschland. Der führende italienische Modekonzern für Herren-, Damen- und Kinderbekleidung OVS setzt dieses Konzept erfolgreich um. Als Teil der Coin Group wurde OVS 1972 gegründet. Die Tochtermarke UPIM agiert bereits seit 1928 in Italien. Kunden bietet das Traditionsunternehmen heute ein digitales Omni‑Kanal‑Erlebnis. Über eine eigens entwickelte App können sie nicht nur online shoppen, sondern im Geschäft beispielsweise die virtuellen Umkleidekabinen nutzen. An der digitalen Wand mit integrierter Kamera und Online-Verbindung schießen sie Selfies, rufen am Touchscreen weitere Produkt-Infos und Verfügbarkeiten anderer Größen ab und bestellen die Wunschkleidung direkt zu sich nach Hause. Hinter dem digitalen Angebot steht eine vernetzte Wertschöpfungskette. OVS hat mit einer Fashion PLM seinen gesamten Produktentwicklungsprozess, vom Design bis hin zur Produktion, umstrukturiert. Die Software-Lösung bündelt alle Daten und Prozesse der Produktlebenszyklen der Kollektionen in einer zentralen Datenplattform. Alle Mitarbeiter arbeiten an unterschiedlichen Standorten zeitgleich und gemeinsam am gleichen Datenstamm. Die Fashion PLM verbessert die Teamarbeit, minimiert Fehler und Aufgabenüberschneidungen, und ermöglicht kürzere Markteinführungszeiten.
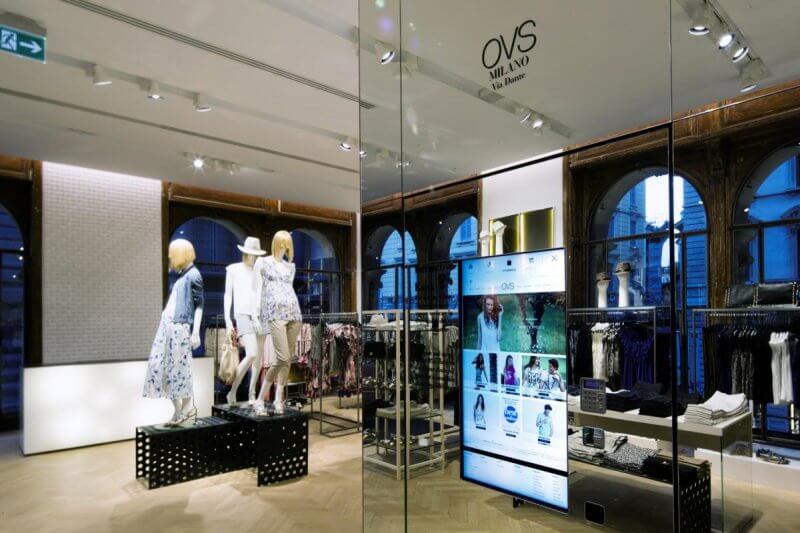
„Noch liegen viele Traditionsunternehmen in der Digitalisierung ihres Geschäftsmodels zurück. Die Umstellung zur digitalen Wertschöpfungskette bringt Vorreitern konkrete Vorteile und Chancen. Nachzügler laufen dagegen Gefahr, den Anschluss endgültig zu verlieren,“ sagt Nicolaes.
Wissen Digital: Smart Factory – Die Produktion von heute
1913 führte Henry Ford in seiner Autofabrik das Fließband ein. Damit revolutionierte er nicht nur die Automobilproduktion, sondern die gesamte industrielle Fertigung. In den 70er Jahren brachte die Weiterentwicklung in Elektronik und Informationstechnologie die Industrie 3.0 mit weiteren Automatisierungen. Heute stehen wir in den Startlöchern für die vierte industrielle Revolution – angetrieben durch den Ruf der Kunden nach qualitativ hochwertigen, individualisierbaren und dennoch erschwinglichen Produkten, ermöglicht durch Digitalisierung, Vernetzung und intelligente Automatisierung. Audi zeigt heute, wie die Produktion von morgen aussieht – in einer Smart Factory.
Auto nach Maß
Führerlos fährt die Karosserie des aktuellen Sportwagen R8 durch das Werk in Neckarsulm, denn Fords Fließband ist aus der Smart Factory verschwunden. Es ist fahrerlosen Transportfahrzeugen, kurz FTF, gewichen, die durch die Produktionshalle fahren. Sie dienen auch als Hebebühne und heben die Karosserie selbstständig bis auf mehr als 1,2 Meter. Mit Hilfe präziser Sensoren orientieren sich die FTF an Umgebungsmerkmalen sowie an Radiofrequenz-Identifikations-Marken, sogenannten RFID-Chips. Die unterschiedlichen Montageschritte werden an 200 modularen Montageinseln durchgeführt. Dieser Aufbau der Produktion gibt den dortigen Mitarbeiterteams mehr Freiraum und Flexibilität, da er eine dynamische Taktung pro Insel je nach Arbeitsaufwand zulässt. Die Teams müssen ihre Arbeit nicht mehr an die Geschwindigkeit des Fließbands anpassen. Ist eine Montageinsel nicht erforderlich, weil der Kunde beispielsweise keine Sitzheizung bestellt hat, umfährt das FTF diese Station. Jedes einzelne Auto wird passgenau nach den Wünschen des Kunden zusammengestellt.
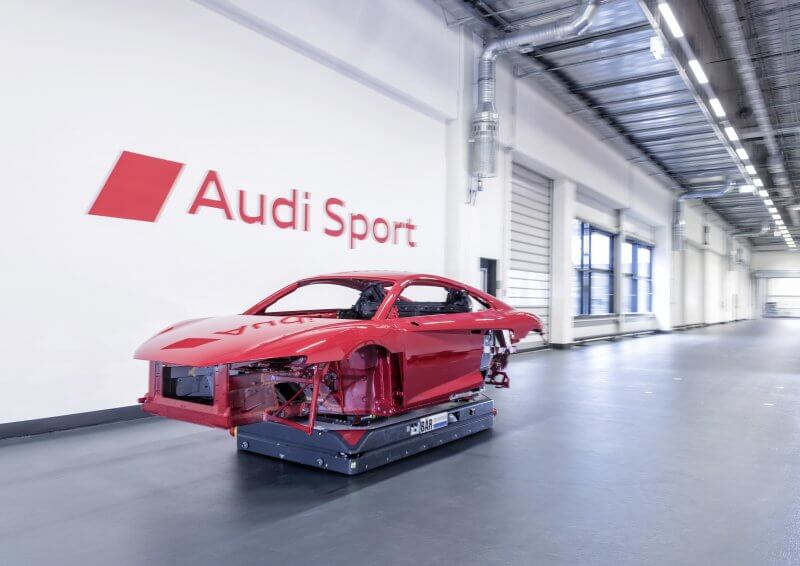
20 Prozent produktiver
Taucht ein Problem an einer der Montageinseln auf, steht damit nicht mehr die gesamte Montage still. Das FTF fährt autonom eine alternative Station an. Die Umstellung auf ein neues Modell ist denkbar einfach. Es werden die notwendigen Inseln für die zusätzlichen Arbeitsschritte aufgebaut, in das System eingebunden und schon ist die Produktion im Gange. Dadurch wird die gesamte Produktion flexibler und um rund 20 Prozent produktiver. Geleitet wird der Produktionsablauf von einem zentralen Steuerungssystem. Es ist mit allen Transportfahrzeugen vernetzt und kommuniziert mit den Montageinseln. Dadurch erkennt es, welche Arbeitsinsel gerade fertig geworden ist und leitet das nächste autonome Transportfahrzeug dorthin.
In einer Smart Factory kommen unterschiedlichste moderne Technologien zum Einsatz. Drohnen fliegen durch die Werkshallen, erledigen schnelle Aufträge und bringen einzelne Ersatzteile zu den Montagestationen. 3D-Metall-Laserdrucker fertigen komplexe Werksmaterialien aus Alu-Staub und neue Mitarbeiter erlernen neue Arbeitsschritte mit Hilfe von Virtual-Reality-Datenbrillen. Die Produktion in der Industrie 4.0 ist digital, vernetzt, intelligent gesteuert – und heute schon Realität.
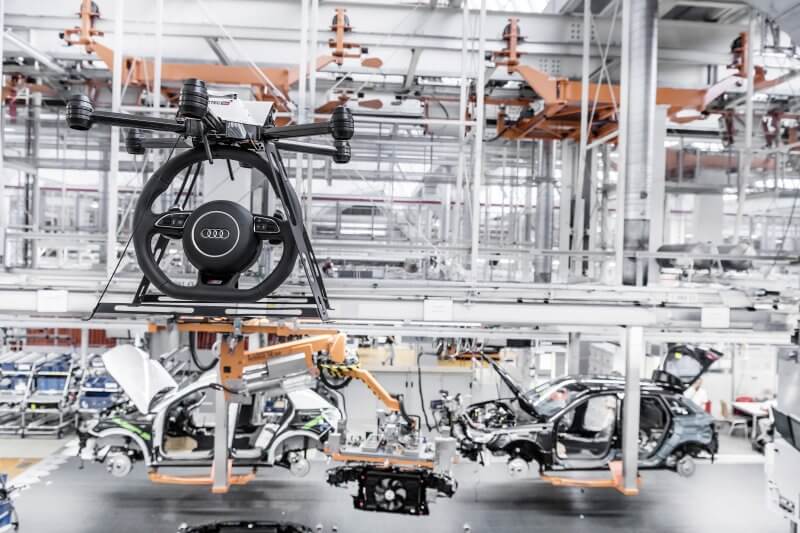
Den gesamten Themendienst zum Download als PDF.